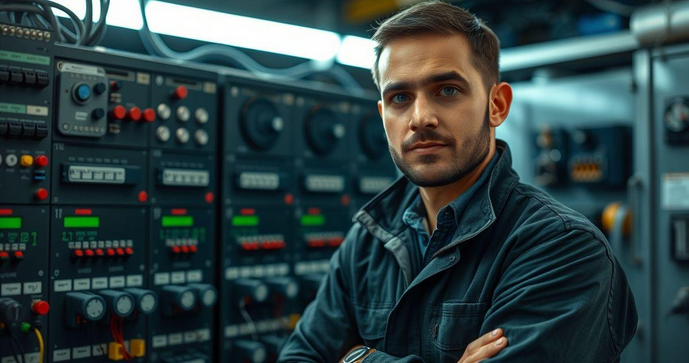
Importância da Manutenção Preventiva em CLPs
A manutenção preventiva em Controladores Lógicos Programáveis (CLPs) desempenha um papel fundamental na garantia de operação contínua e eficiente em sistemas automatizados. Essa prática visa identificar e corrigir problemas potenciais antes que causem falhas maiores.
Ao implementar um cronograma de manutenção preventiva, as empresas podem prolongar a vida útil dos CLPs e evitar paradas não programadas, que podem resultar em custos significativos. O tempo de inatividade pode impactar a produtividade e a eficiência operacional, levando a perdas financeiras.
Além disso, a manutenção preventiva contribui para a segurança do ambiente de trabalho. CLPs que não recebem manutenção adequada podem falhar em momentos críticos, colocando em risco a segurança dos equipamentos e dos trabalhadores.
Outra vantagem importante da manutenção preventiva é a possibilidade de otimização do desempenho dos sistemas controlados pelos CLPs. O monitoramento e a atualização regulares permitem identificar áreas de melhoria, ajustando programas e configurações para maximizar a eficiência.
Por fim, a manutenção preventiva facilita a conformidade com regulamentos e normas industriais. Muitas indústrias são obrigadas a seguir certificações que requerem manutenção regular dos equipamentos, garantindo não apenas a segurança, mas também a qualidade do processo produtivo.
Tipos de Manutenção: Corretiva, Preventiva e Preditiva
Existem três tipos principais de manutenção que são fundamentais para o funcionamento eficaz dos Controladores Lógicos Programáveis (CLPs): a manutenção corretiva, a manutenção preventiva e a manutenção preditiva. Cada uma delas desempenha um papel específico na gestão e otimização dos sistemas automatizados.
A manutenção corretiva é realizada após a identificação de uma falha no sistema. Ela visa reparar ou substituir componentes danificados para restaurar a operação normal do CLP. Embora seja necessária, essa abordagem pode resultar em paradas inesperadas, aumentando o tempo de inatividade e os custos operacionais.
A manutenção preventiva, por sua vez, é um método proativo que envolve a realização de inspeções e serviços regulares nos CLPs antes que ocorram falhas. O objetivo é garantir que os sistemas funcionem corretamente e que problemas potenciais sejam resolvidos antes que se tornem críticos. Isso não apenas aumenta a confiabilidade dos sistemas, mas também maximiza sua vida útil.
A manutenção preditiva utiliza tecnologias avançadas, como sensores e análise de dados, para monitorar o desempenho dos CLPs em tempo real. Esta abordagem permite prever quando uma falha pode ocorrer, possibilitando intervenções programadas. Dessa forma, as empresas podem efetuar manutenções de maneira mais eficiente, reduzindo os custos e melhorando a disponibilidade dos sistemas.
Compreender as diferenças entre esses tipos de manutenção é essencial para a gestão eficaz dos sistemas automatizados. Juntas, elas formam uma estratégia abrangente que assegura a operação contínua e eficaz dos CLPs, minimizando perdas financeiras e riscos ocupacionais.
Ferramentas Necessárias para Manutenção de CLPs
A manutenção eficaz de Controladores Lógicos Programáveis (CLPs) requer um conjunto específico de ferramentas que facilitam a inspeção, o diagnóstico e a execução de reparos. A utilização dessas ferramentas é essencial para garantir que as intervenções sejam feitas de maneira precisa e eficiente.
Entre as ferramentas indispensáveis, encontram-se os multímetros. Esses dispositivos permitem a medição de tensão, corrente e resistência, sendo essenciais para verificar as condições elétricas dos circuitos do CLP. Um multímetro de boa qualidade pode auxiliar na identificação de problemas diversos, desde falhas de conexão até componentes defeituosos.
Outra ferramenta importante é o software de programação e diagnóstico especializado. Este tipo de software é utilizado para modificar as configurações do CLP, atualizar firmware e realizar testes de funcionalidade. Com ele, os técnicos podem também monitorar o desempenho do sistema em tempo real, facilitando a detecção de anomalias.
Chaves de fenda e chaves inglesas são ferramentas manuais essenciais para a montagem e desmontagem de componentes do CLP. Além disso, o uso de ferramentas de crimpagem é necessário para garantir conexões adequadas nos cabos que interagem com o sistema.
Os scanners de código de barras e leitores de código de barras também podem ser úteis em ambientes automatizados, pois permitem a identificação rápida de peças sobressalentes e componentes relevantes, otimizando o gerenciamento de estoque durante a manutenção.
Por fim, ter acesso a um kit de limpeza, que inclua pincéis e produtos químicos adequados, é vital para a manutenção preventiva. A limpeza regular de componentes eletrônicos ajuda a prevenir falhas causadas por poeira e contaminantes, garantindo que o CLP opere em condições ideais.
Etapas da Manutenção de CLPs: Passo a Passo
A manutenção de Controladores Lógicos Programáveis (CLPs) deve seguir um conjunto estruturado de etapas para garantir que os sistemas funcionem perfeitamente e sem interrupções. Abaixo estão as etapas principais da manutenção, apresentadas de forma clara e objetiva.
1. Planejamento da Manutenção: Antes de iniciar qualquer tarefa, é necessário elaborar um plano de manutenção que inclua a definição das atividades a serem executadas, a programação das tarefas, e a alocação das ferramentas e materiais necessários. Este planejamento é fundamental para evitar interrupções no processo produtivo.
2. Desligamento Seguro: Garantir a segurança é a prioridade. Antes de realizar qualquer trabalho no CLP, é preciso desconectar a fonte de energia e sinalizar a área para evitar acidentes. Essa etapa é crucial para proteger os operadores e os equipamentos.
3. Inspeção Visual: Realizar uma inspeção visual detalhada no CLP para identificar sinais de desgaste, componentes danificados ou qualquer anomalia visível. A verificação de conexões, fiações e condições físicas do equipamento é essencial para o diagnóstico correto.
4. Testes Funcionais: Após a inspeção, proceder com testes funcionais para verificar se o CLP está operando dentro dos parâmetros especificados. Isso pode incluir a revisão de programas, a execução de ciclos de operação e a validação de saídas e entradas.
5. Limpeza: Realizar a limpeza dos componentes, incluindo a remoção de poeira e detritos que possam afetar a performance do CLP. A limpeza deve ser feita com produtos adequados e técnicas corretas para não danificar os circuitos ou a carcaça.
6. Execução de Manutenção Preventiva: Executar as ações previstas no plano de manutenção, como a lubrificação de partes móveis, a substituição de peças desgastadas e a atualização de software, se necessário. Essas ações visam prevenir falhas futuras.
7. Documentação: É importante registrar todas as atividades realizadas durante a manutenção, incluindo resultados de testes, peças substituídas e qualquer outra observação pertinente. Essa documentação é vital para o histórico do equipamento e para futuras manutenções.
8. Reinicialização e Testes Finais: Após concluir a manutenção, reiniciar o CLP e realizar novos testes para assegurar que tudo está funcionando conforme o esperado. Isso garante que a manutenção foi efetiva e que o sistema está pronto para operação.
Sinais de Que o CLP Precisa de Manutenção
Reconhecer os sinais de que um Controlador Lógico Programável (CLP) precisa de manutenção é essencial para evitar falhas que possam comprometer a operação dos sistemas automatizados. Abaixo estão alguns sinais comuns que indicam a necessidade de intervenção.
1. Falhas Frequentes: Se o CLP apresenta erros ou falhas constantes nas operações, como interrupções inesperadas, isso pode ser um sinal de que componentes internos estão desgastados ou com defeito, exigindo uma revisão imediata.
2. Desempenho Lento: Um desempenho abaixo do esperado, com respostas lentas ou atrasos nas operações, pode indicar que o CLP necessita de manutenção. Esse sinal pode ser resultado de sobrecarga de trabalho ou problemas de hardware.
3. Alarmes e Mensagens de Erro: A presença contínua de alarmes ou mensagens de erro no painel de controle do CLP é um indicador claro de que algo está errado. É fundamental investigar essas notificações para determinar a causa raiz do problema.
4. Calor Excessivo: Se o CLP está superaquecendo, isso pode ser um sinal de problemas internos, como falhas em ventoinhas ou dissipadores de calor obstruídos. O superaquecimento pode danificar componentes internos e deve ser abordado rapidamente.
5. Ruídos Incomuns: Barulhos estrondosos ou anormais provenientes do CLP podem indicar falhas mecânicas, desgastes nos componentes ou problemas elétricos. Qualquer ruído fora do comum deve ser verificado imediatamente.
6. Conexões Soltas: Se você notar que os cabos estão soltos ou mal conectados, isso pode causar falhas intermitentes no funcionamento do CLP. As conexões devem ser revisadas e ajustadas sempre que necessário.
7. Alterações no Ambiente: Mudanças nas condições ambientais, como um aumento na umidade ou na temperatura, podem afetar o desempenho do CLP. Nesses casos, é importante garantir que o sistema esteja protegido e, se necessário, realizar manutenções preventivas.
8. Dificuldades na Comunicação: Se o CLP enfrenta problemas para se comunicar com outros dispositivos ou sistemas na rede, isso pode ser um indicativo de falhas em conexões ou problemas de software, que precisam ser diagnosticados.
Impactos da Falta de Manutenção em Sistemas Automatizados
A falta de manutenção em Controladores Lógicos Programáveis (CLPs) e sistemas automatizados pode ter consequências significativas e adversas, impactando não apenas a operação dos sistemas, mas também a segurança e a eficiência operacional. Abaixo estão alguns dos principais impactos da negligência na manutenção.
1. Aumento do Tempo de Inatividade: A ausência de manutenção preventiva pode resultar em falhas inesperadas que exigem reparos emergenciais. Isso gera um aumento no tempo de inatividade do sistema, resultando em paradas na produção e perda de eficiência.
2. Custos Elevados de Reparação: Quando um CLP falha devido à falta de cuidados, os custos de reparo costumam ser significativamente maiores do que aqueles relacionados a manutenções preventivas regulares. Equipamentos danificados podem necessitar de peças de reposição dispendiosas e mão de obra especializada.
3. Comprometimento da Qualidade do Produto: Sistemas automatizados que não estão devidamente mantidos podem produzir produtos com qualidade inferior. Isso pode impactar negativamente a reputação da empresa e resultar em reclamações de clientes, gerando problemas de relacionamento e perda de mercado.
4. Aumento do Desgaste de Equipamentos: Equipamentos que não são regularmente verificados e ajustados tendem a sofrer desgastes mais rápidos. Isso reduz a vida útil dos componentes, exigindo substituições mais frequentes e aumentando significativamente os custos operacionais.
5. Riscos à Segurança: Sistemas automatizados que não passam por manutenções regulares podem operar de forma insegura, colocando em risco a integridade dos operadores e do ambiente. Falhas em segurança, como dispositivos de parada de emergência que não funcionam, podem levar a acidentes sérios.
6. Dificuldades em Conforming-se a Normas e Regulamentações: Muitas indústrias são obrigadas a seguir normas de segurança e regulamentações que exigem manutenções periódicas. A não conformidade pode resultar em multas e penalidades, além de afetar a credibilidade da empresa.
7. Implicações para a Produtividade: A ineficiência resultante da falta de manutenção pode levar a uma produção menor, afetando as metas e os prazos estabelecidos. Essa redução na produtividade pode impactar a capacidade da empresa de atender aos pedidos de clientes em tempo hábil.
8. Dificuldade em Adotar Novas Tecnologias: Sistemas que não são mantidos adequadamente podem se tornar obsoletos, dificultando a adaptação a novas tecnologias. A incapacidade de integrar novos sistemas pode limitar as oportunidades de inovação e crescimento.
A manutenção adequada de Controladores Lógicos Programáveis (CLPs) é vital para garantir a eficiência, segurança e longevidade dos sistemas automatizados.
Através de práticas regulares, como a manutenção preventiva e a utilização das ferramentas corretas, as empresas podem evitar falhas dispendiosas e garantir operações contínuas.
Ignorar a importância da manutenção não apenas compromete o desempenho dos sistemas, mas também pode levar a custos elevados, problemas de segurança e perda de qualidade nos produtos.
Investir em manutenções regulares é, portanto, um passo essencial para maximizar a produtividade e a sustentabilidade dos processos industriais.
Gostou? compartilhe!