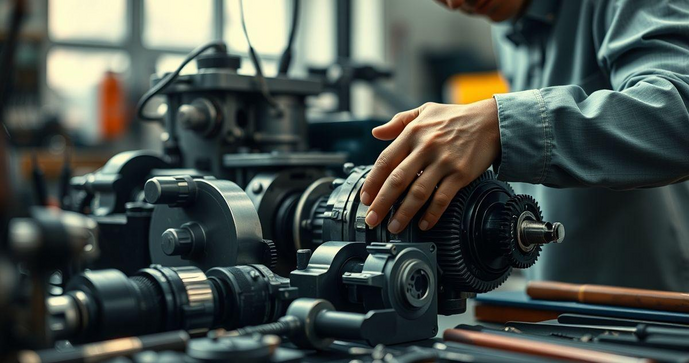
A manutenção preventiva e corretiva de equipamentos é fundamental para garantir a eficiência operacional e a durabilidade dos ativos em qualquer setor. Com a crescente demanda por produtividade e redução de custos, entender as diferenças entre esses dois tipos de manutenção se torna essencial. Neste artigo, abordaremos a importância da manutenção, as melhores práticas a serem adotadas e como monitorar a eficácia das ações implementadas.
Importância da Manutenção Preventiva para Equipamentos
A manutenção preventiva é uma estratégia essencial para garantir o funcionamento eficiente e a longevidade dos equipamentos em diversos setores, como industrial, comercial e de serviços. Ao contrário da manutenção corretiva, que é realizada após a ocorrência de falhas, a manutenção preventiva busca evitar problemas antes que eles aconteçam. Essa abordagem proativa não apenas minimiza o tempo de inatividade, mas também reduz custos operacionais e melhora a segurança no ambiente de trabalho.
Um dos principais benefícios da manutenção preventiva é a redução de falhas inesperadas. Equipamentos que passam por inspeções regulares e manutenção programada têm menor probabilidade de apresentar problemas graves. Isso é especialmente importante em indústrias onde a interrupção da produção pode resultar em perdas financeiras significativas. Por exemplo, uma falha em uma máquina pode levar a paradas prolongadas, afetando toda a linha de produção e resultando em atrasos nas entregas.
Além disso, a manutenção preventiva contribui para a eficiência energética dos equipamentos. Equipamentos mal mantidos tendem a consumir mais energia, o que não apenas aumenta os custos operacionais, mas também impacta negativamente o meio ambiente. Ao realizar manutenções regulares, é possível identificar e corrigir problemas que podem estar causando desperdício de energia, como peças desgastadas ou mal ajustadas. Isso resulta em um funcionamento mais eficiente e sustentável.
Outro aspecto importante da manutenção preventiva é a segurança. Equipamentos que não são mantidos adequadamente podem representar riscos significativos para os operadores e para o ambiente de trabalho. Por exemplo, máquinas com peças soltas ou desgastadas podem causar acidentes, colocando em risco a integridade física dos colaboradores. A manutenção preventiva ajuda a identificar e corrigir esses problemas antes que se tornem perigosos, promovendo um ambiente de trabalho mais seguro.
Além de prevenir falhas e garantir a segurança, a manutenção preventiva também pode prolongar a vida útil dos equipamentos. Quando os equipamentos são mantidos em boas condições, eles tendem a durar mais, o que significa que as empresas não precisam investir constantemente em novos ativos. Isso resulta em uma economia significativa a longo prazo. Por exemplo, um Ihm rockwell bem mantido pode operar de forma eficaz por muitos anos, enquanto um que não recebe a devida atenção pode precisar ser substituído muito mais cedo.
Além disso, a manutenção preventiva pode melhorar a qualidade dos produtos ou serviços oferecidos. Equipamentos que funcionam corretamente produzem resultados mais consistentes e de maior qualidade. Isso é especialmente relevante em setores como a manufatura, onde a precisão e a qualidade são cruciais. Quando os equipamentos estão em boas condições, as empresas podem garantir que seus produtos atendam aos padrões de qualidade exigidos pelo mercado, aumentando a satisfação do cliente e a reputação da marca.
Implementar um programa de manutenção preventiva também pode resultar em uma melhor gestão de recursos. Ao planejar e agendar manutenções, as empresas podem otimizar o uso de suas equipes e equipamentos. Isso significa que os recursos são utilizados de forma mais eficiente, reduzindo o tempo ocioso e aumentando a produtividade geral. Além disso, a manutenção preventiva permite que as empresas se preparem melhor para as demandas futuras, ajustando seus planos de manutenção conforme necessário.
Por fim, a manutenção preventiva pode ser um diferencial competitivo. Empresas que investem em manutenção regular e eficaz tendem a se destacar no mercado. A capacidade de operar de forma contínua e eficiente, sem interrupções inesperadas, pode ser um fator decisivo para os clientes na hora de escolher um fornecedor. Portanto, a manutenção preventiva não é apenas uma questão de eficiência operacional, mas também uma estratégia de negócios inteligente.
Em resumo, a importância da manutenção preventiva para equipamentos não pode ser subestimada. Ela não apenas ajuda a evitar falhas e a garantir a segurança, mas também prolonga a vida útil dos ativos, melhora a eficiência energética e a qualidade dos produtos. Ao implementar um programa de manutenção preventiva, as empresas podem otimizar seus recursos, aumentar a produtividade e se destacar no mercado. Investir em manutenção preventiva é, sem dúvida, uma decisão estratégica que traz benefícios significativos a longo prazo.
Diferenças entre Manutenção Preventiva e Corretiva
A manutenção de equipamentos é uma parte crucial da gestão de ativos em qualquer organização. Entre as estratégias mais comuns estão a manutenção preventiva e a manutenção corretiva. Embora ambas tenham o objetivo de garantir o funcionamento adequado dos equipamentos, elas diferem significativamente em suas abordagens, benefícios e impactos operacionais. Compreender essas diferenças é fundamental para que as empresas possam implementar a estratégia mais eficaz para suas necessidades.
A manutenção preventiva é uma abordagem proativa que envolve a realização de inspeções regulares, ajustes e substituições de peças antes que ocorram falhas. O principal objetivo é evitar que os equipamentos quebrem ou apresentem problemas que possam interromper a operação. Essa estratégia é baseada em um cronograma de manutenção, que pode ser definido com base em recomendações do fabricante, histórico de falhas e condições de operação. Por exemplo, a troca de lubrificantes, a verificação de componentes e a calibração de máquinas são atividades típicas da manutenção preventiva.
Por outro lado, a manutenção corretiva é uma abordagem reativa. Ela é realizada após a ocorrência de uma falha ou problema no equipamento. O foco da manutenção corretiva é restaurar o funcionamento do equipamento o mais rápido possível. Isso pode envolver reparos, substituições de peças danificadas ou até mesmo a realização de consertos mais complexos. Um exemplo comum de manutenção corretiva é o conserto de placas eletrônicas que falharam em um sistema de controle, exigindo uma intervenção imediata para evitar paradas na produção.
Uma das principais diferenças entre as duas abordagens é o custo. A manutenção preventiva, embora possa envolver investimentos regulares em inspeções e serviços, tende a ser mais econômica a longo prazo. Isso ocorre porque ela ajuda a evitar falhas graves que podem resultar em custos elevados de reparo e perda de produção. Em contraste, a manutenção corretiva pode ser muito mais cara, especialmente se a falha ocorrer em um momento crítico, resultando em paradas não planejadas e perda de receita.
Além disso, a manutenção preventiva contribui para a eficiência operacional. Equipamentos que são mantidos regularmente tendem a operar de forma mais eficiente, consumindo menos energia e apresentando menos problemas. Isso não apenas melhora a produtividade, mas também pode resultar em uma redução nos custos operacionais. Por outro lado, a manutenção corretiva pode levar a um aumento no tempo de inatividade e na ineficiência, já que os equipamentos podem não estar funcionando em sua capacidade ideal após um reparo.
Outro aspecto importante a considerar é a segurança. A manutenção preventiva ajuda a identificar e corrigir problemas antes que eles se tornem perigosos. Por exemplo, uma máquina que não é mantida adequadamente pode apresentar riscos de segurança para os operadores. A manutenção corretiva, por sua vez, pode resultar em situações de risco, especialmente se a falha ocorrer durante a operação. Isso pode levar a acidentes e lesões, aumentando a importância da manutenção preventiva em ambientes de trabalho.
Além disso, a manutenção preventiva permite um melhor planejamento e gestão de recursos. Com um cronograma de manutenção bem definido, as empresas podem programar paradas para manutenção em momentos que minimizam o impacto nas operações. Isso facilita a alocação de recursos e a programação de trabalho, permitindo que as equipes se preparem adequadamente para as atividades de manutenção. Em contraste, a manutenção corretiva muitas vezes resulta em interrupções inesperadas, dificultando o planejamento e a gestão de recursos.
Em termos de impacto na vida útil dos equipamentos, a manutenção preventiva é geralmente mais benéfica. Equipamentos que recebem manutenção regular tendem a ter uma vida útil mais longa, enquanto aqueles que dependem exclusivamente da manutenção corretiva podem apresentar um desgaste mais rápido. Isso significa que, a longo prazo, a manutenção preventiva pode resultar em uma economia significativa, já que as empresas não precisarão substituir equipamentos com tanta frequência.
Por fim, a cultura organizacional também pode ser afetada pelas abordagens de manutenção. Empresas que adotam a manutenção preventiva tendem a promover uma cultura de proatividade e responsabilidade, onde os colaboradores estão mais conscientes da importância da manutenção e do cuidado com os equipamentos. Em contrapartida, uma abordagem predominantemente corretiva pode levar a uma cultura reativa, onde os problemas são tratados apenas quando surgem, o que pode resultar em um ambiente de trabalho menos eficiente e mais estressante.
Em resumo, as diferenças entre manutenção preventiva e corretiva são significativas e impactam diretamente a eficiência operacional, os custos, a segurança e a vida útil dos equipamentos. Enquanto a manutenção preventiva é uma abordagem proativa que busca evitar falhas e otimizar o desempenho, a manutenção corretiva é reativa e se concentra em resolver problemas após sua ocorrência. Para as empresas, a escolha entre essas duas abordagens deve ser baseada em uma análise cuidadosa de suas necessidades, recursos e objetivos operacionais.
Melhores Práticas para Implementar Manutenção de Equipamentos
A implementação de um programa eficaz de manutenção de equipamentos é essencial para garantir a eficiência operacional e a longevidade dos ativos em qualquer organização. A manutenção adequada não apenas previne falhas, mas também melhora a segurança e a produtividade. Para alcançar esses objetivos, é importante seguir algumas melhores práticas que podem otimizar o processo de manutenção. A seguir, discutiremos as principais estratégias para implementar a manutenção preventiva e corretiva de equipamentos de forma eficaz.
Uma das primeiras etapas para implementar um programa de manutenção eficaz é realizar um inventário detalhado de todos os equipamentos. Conhecer a localização, a condição e as especificações de cada ativo é fundamental para planejar a manutenção. Esse inventário deve incluir informações sobre a idade dos equipamentos, o histórico de manutenção e as recomendações do fabricante. Com esses dados em mãos, as empresas podem priorizar quais equipamentos precisam de mais atenção e quais podem ser mantidos em um cronograma de manutenção regular.
Após a realização do inventário, o próximo passo é desenvolver um cronograma de manutenção. Este cronograma deve incluir as atividades de manutenção preventiva, como inspeções regulares, lubrificação, ajustes e substituições de peças. É importante que o cronograma seja realista e leve em consideração a carga de trabalho da equipe e a disponibilidade dos equipamentos. Além disso, as manutenções devem ser programadas em momentos que minimizem o impacto nas operações, evitando interrupções desnecessárias.
Outra prática recomendada é a capacitação da equipe de manutenção. Investir em treinamento e desenvolvimento para os colaboradores é essencial para garantir que eles tenham as habilidades e conhecimentos necessários para realizar a manutenção de forma eficaz. Isso inclui não apenas o conhecimento técnico sobre os equipamentos, mas também a compreensão das melhores práticas de segurança. Uma equipe bem treinada é mais capaz de identificar problemas antes que se tornem críticos e de realizar reparos de forma eficiente.
Além disso, a utilização de tecnologia pode ser um grande aliado na implementação de um programa de manutenção eficaz. Sistemas de gestão de manutenção computadorizada (CMMS) podem ajudar a organizar e monitorar as atividades de manutenção, facilitando o agendamento, o registro de histórico e a geração de relatórios. Esses sistemas permitem que as empresas acompanhem o desempenho dos equipamentos e identifiquem tendências que podem indicar a necessidade de manutenção adicional. A tecnologia também pode ser utilizada para implementar a manutenção preditiva, que utiliza dados e análises para prever falhas antes que elas ocorram.
Outra prática importante é a realização de auditorias regulares do programa de manutenção. Essas auditorias ajudam a avaliar a eficácia das atividades de manutenção e a identificar áreas que precisam de melhorias. Durante as auditorias, é fundamental revisar o histórico de manutenção, verificar se as atividades programadas estão sendo realizadas e avaliar a condição dos equipamentos. Com base nos resultados das auditorias, as empresas podem ajustar seus cronogramas e processos de manutenção para garantir que estejam atendendo às necessidades operacionais.
A comunicação também desempenha um papel crucial na implementação de um programa de manutenção eficaz. É importante que todos os colaboradores, desde a equipe de manutenção até os operadores de máquinas, estejam cientes das práticas de manutenção e da importância de relatar problemas imediatamente. Criar uma cultura de comunicação aberta e transparente ajuda a garantir que os problemas sejam identificados e resolvidos rapidamente, evitando falhas maiores no futuro.
Além disso, a documentação adequada é uma parte essencial do processo de manutenção. Manter registros detalhados de todas as atividades de manutenção, incluindo datas, tipos de serviços realizados e peças substituídas, é fundamental para monitorar o desempenho dos equipamentos ao longo do tempo. Esses registros não apenas ajudam a identificar padrões de falhas, mas também são úteis para auditorias e para garantir a conformidade com as normas de segurança e regulamentações.
Por fim, é importante considerar a manutenção como um investimento e não apenas um custo. Embora a implementação de um programa de manutenção possa exigir recursos financeiros e tempo, os benefícios a longo prazo superam amplamente os custos iniciais. Equipamentos bem mantidos têm uma vida útil mais longa, operam de forma mais eficiente e apresentam menos falhas, resultando em economias significativas para a empresa. Portanto, é fundamental que as organizações reconheçam a importância da manutenção e se comprometam a implementar as melhores práticas para garantir o sucesso de seus programas de manutenção.
Em resumo, a implementação de um programa eficaz de manutenção de equipamentos envolve várias melhores práticas, incluindo a realização de um inventário detalhado, o desenvolvimento de um cronograma de manutenção, a capacitação da equipe, a utilização de tecnologia, a realização de auditorias regulares, a comunicação eficaz e a documentação adequada. Ao seguir essas práticas, as empresas podem garantir que seus equipamentos operem de forma eficiente e segura, maximizando a produtividade e minimizando custos.
Como Monitorar e Avaliar a Eficiência da Manutenção
Monitorar e avaliar a eficiência da manutenção de equipamentos agricolas é uma parte crucial da gestão de ativos em qualquer organização. Um programa de manutenção eficaz não se limita apenas à execução de tarefas, mas também envolve a análise contínua dos resultados dessas atividades. Através de um monitoramento adequado, as empresas podem identificar áreas de melhoria, otimizar processos e garantir que os equipamentos operem em sua máxima eficiência. A seguir, discutiremos as principais estratégias para monitorar e avaliar a eficiência da manutenção.
Uma das primeiras etapas para monitorar a eficiência da manutenção é estabelecer indicadores de desempenho (KPIs). Esses indicadores são métricas que ajudam a medir o sucesso das atividades de manutenção em relação aos objetivos estabelecidos. Alguns KPIs comuns incluem o tempo médio entre falhas (MTBF), o tempo médio para reparo (MTTR), a taxa de falhas e o custo de manutenção por unidade de produção. Ao acompanhar esses indicadores, as empresas podem obter uma visão clara do desempenho de seus equipamentos e da eficácia de suas estratégias de manutenção.
O tempo médio entre falhas (MTBF) é um dos KPIs mais importantes, pois indica a confiabilidade dos equipamentos. Um MTBF elevado sugere que os equipamentos estão funcionando de maneira eficiente e que a manutenção preventiva está sendo eficaz. Por outro lado, um MTBF baixo pode indicar a necessidade de uma revisão nas práticas de manutenção ou na qualidade dos equipamentos. Da mesma forma, o tempo médio para reparo (MTTR) fornece informações sobre a rapidez com que os problemas são resolvidos. Um MTTR baixo é desejável, pois significa que a equipe de manutenção é capaz de responder rapidamente a falhas, minimizando o tempo de inatividade.
Além dos KPIs, a coleta de dados é fundamental para monitorar a eficiência da manutenção. Isso pode ser feito através de sistemas de gestão de manutenção computadorizada (CMMS), que permitem registrar todas as atividades de manutenção, incluindo inspeções, reparos e substituições de peças. Esses sistemas também podem gerar relatórios detalhados que ajudam a identificar tendências e padrões ao longo do tempo. A análise desses dados pode revelar informações valiosas sobre a condição dos equipamentos e a eficácia das estratégias de manutenção implementadas.
Outra prática importante é a realização de auditorias regulares do programa de manutenção. Essas auditorias ajudam a avaliar se as atividades de manutenção estão sendo realizadas conforme o planejado e se estão atingindo os resultados desejados. Durante as auditorias, é fundamental revisar o histórico de manutenção, verificar se as atividades programadas estão sendo cumpridas e avaliar a condição dos equipamentos. Com base nos resultados das auditorias, as empresas podem ajustar seus cronogramas e processos de manutenção para garantir que estejam atendendo às necessidades operacionais.
A comunicação entre as equipes de manutenção e operação também é essencial para monitorar a eficiência da manutenção. Os operadores de máquinas são frequentemente os primeiros a perceber problemas e podem fornecer informações valiosas sobre o desempenho dos equipamentos. Criar um canal de comunicação aberto e eficaz entre as equipes ajuda a garantir que os problemas sejam identificados e relatados rapidamente, permitindo que a equipe de manutenção tome as medidas necessárias antes que as falhas se tornem críticas.
Além disso, a implementação de um programa de manutenção preditiva pode ser uma estratégia eficaz para monitorar a eficiência da manutenção. A manutenção preditiva utiliza dados e análises para prever falhas antes que elas ocorram, permitindo que as empresas realizem manutenções programadas com base na condição real dos equipamentos. Isso não apenas ajuda a evitar falhas inesperadas, mas também otimiza o uso de recursos, pois as manutenções são realizadas apenas quando necessário.
Outra abordagem valiosa é a comparação de desempenho com benchmarks do setor. As empresas podem comparar seus KPIs de manutenção com os de outras organizações do mesmo setor para identificar áreas de melhoria. Essa análise comparativa pode revelar práticas de manutenção que estão funcionando bem em outras empresas e que podem ser adaptadas para melhorar a eficiência na própria organização.
Por fim, a avaliação da eficiência da manutenção deve ser um processo contínuo. As empresas devem estar dispostas a revisar e ajustar suas estratégias de manutenção com base nos dados coletados e nas análises realizadas. Isso pode incluir a atualização de cronogramas de manutenção, a implementação de novas tecnologias ou a reavaliação das práticas de treinamento da equipe. A flexibilidade e a disposição para se adaptar são fundamentais para garantir que o programa de manutenção permaneça eficaz ao longo do tempo.
Em resumo, monitorar e avaliar a eficiência da manutenção é essencial para garantir que os equipamentos operem de forma eficiente e segura. Estabelecer KPIs, coletar dados, realizar auditorias regulares, promover a comunicação entre equipes e implementar manutenção preditiva são algumas das melhores práticas que podem ajudar as empresas a otimizar seus programas de manutenção. Ao seguir essas estratégias, as organizações podem não apenas melhorar a eficiência de seus equipamentos, mas também reduzir custos e aumentar a produtividade. A manutenção eficaz é um investimento que traz retornos significativos a longo prazo, garantindo que os ativos da empresa estejam sempre em condições ideais de operação.
Em conclusão, a manutenção preventiva e corretiva de equipamentos desempenha um papel crucial na eficiência operacional e na longevidade dos ativos. Compreender as diferenças entre essas abordagens permite que as empresas adotem estratégias adequadas para suas necessidades específicas. Ao implementar melhores práticas de manutenção e monitorar continuamente a eficácia das ações, as organizações podem não apenas evitar falhas e reduzir custos, mas também garantir um ambiente de trabalho mais seguro e produtivo. Investir em um programa de manutenção robusto é, portanto, uma decisão estratégica que traz benefícios significativos a longo prazo, contribuindo para o sucesso e a competitividade no mercado.
Gostou? compartilhe!